
Finally, there are systems where the solid and liquid are insoluble, such as W–Cu, so solid-skeleton sintering determines the densification rate. This is how mixed copper and tin powders are used to fabricate porous bronze bearings. In another variant, a transient liquid forms and dissolves into the solid over time. This approach is used to sinter tool steels. The WC–Co system is a prime example, where the eutectic at 1310 ☌ enables the bonding of micrometer size WC grains into a dense component, such as a drill or cutting insert.īesides mixed powders, LPS is possible using alloy powders that partially melt to form a semisolid structure.
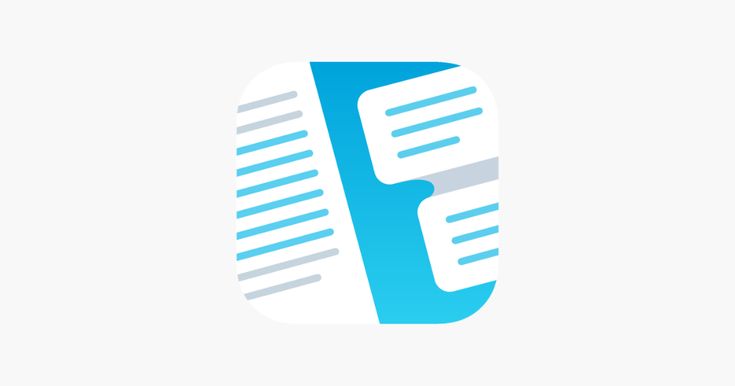
The LPS events are ideal for densifying hard materials that cannot be fabricated using other manufacturing approaches. The surface energy associated with pores leads to their annihilation, while there is progressive microstructure coarsening and bonding to increase rigidity. Further, because of solid solubility in the liquid, the liquid improves transport rates responsible for grain coarsening and densification. In this case, the newly formed liquid penetrates between the solid grains, dissolves the sinter bonds, and induces grain rearrangement. The common situation is for the liquid to wet the solid. Depending on the solid–liquid solubility relations, different microstructure evolution pathways are possible. The solid grains undergo solid-state sintering during heating. The publication rate accelerated as applications emerged, and today articles on LPS and liquid phase sintered products exceed 100,000 contributions.įrom these efforts emerge a conceptual view of the events taking place, as sketched in Fig. published a brief book on the subject and a more detailed treatment followed in 1985. Cannon and Lenel provided a qualitative conceptualization, while Kingery provided a quantitative treatment.

Qualitative models emerged over the next 20 years based on observations from a variety of systems. The LPS mechanistic conceptualization started with the work of Price et al.
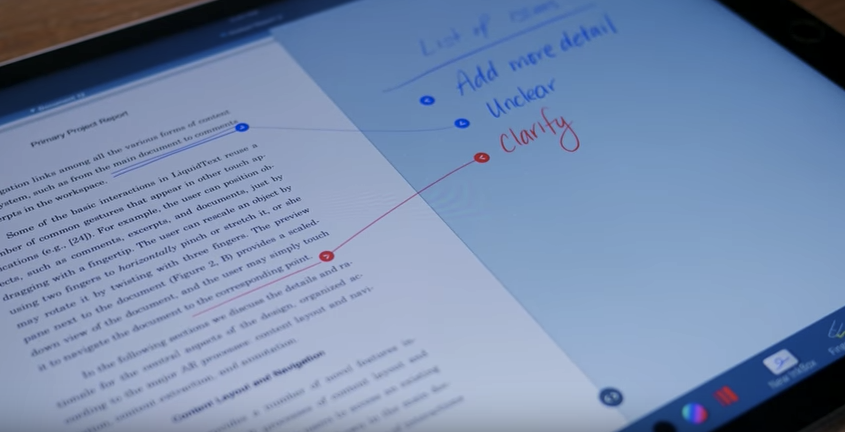
Over the next 70 years, LPS processing spread to a diverse range of applications-oil well drilling tips, porcelain jacketed dental crowns, automotive valve seats, wire drawing dies, high-temperature bearings, electrical contacts, electronic capacitors, radiation shields, diesel engine turbochargers, electronic insulator substrates, golf clubs balance weights, ultrasonic transducers, electronic solders, and grinding abrasives, as examples. Important technical advances in LPS came in the 1930s with the development of several materials cemented carbides (WC–Co), porous bronze (Cu–Sn), tungsten heavy alloys (W–Ni–Cu), copper steels (Fe–Cu–C), and cermets (TiC-Fe). In some ceramic compositions, the liquid phase is a viscous glass, but for this treatment we refer to it as a liquid. At high temperatures, the glass turns into a viscous liquid early porcelain was a widely valued example. Since the final product is a composite with customized properties, LPS is the dominant commercial sintering process.Įarly uses of LPS involved firing ceramics with a glass bond. High-diffusion rates are associated with liquids, giving fast sintering or lower sintering temperatures. At the same time, the high temperature softens the solid, further assisting densification. This solubility causes the liquid to wet the solid, providing a capillary force that pulls the grains together. In the typical situation, the solid grains are soluble in the liquid. Liquid phase sintering (LPS) is applied to alloys and composites that melt over a range of temperatures.
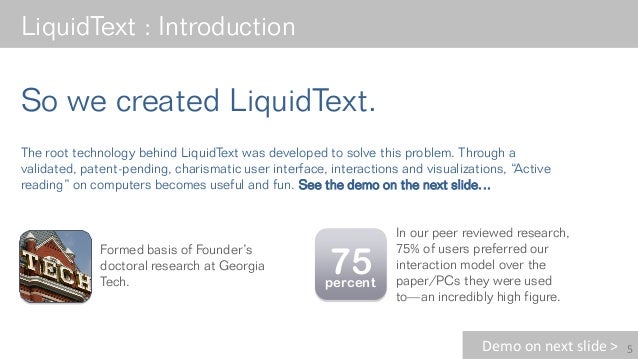
Snow sinters to form ice at temperatures near −15 ☌, while alumina requires temperatures in excess of 1000 ☌.Ī widely applied variant relies on forming a liquid during the sintering cycle. For solid-state sintering, it is appropriate to think of sintering with respect to the melting temperature. It takes place faster as the particle size decreases, since diffusion distances are shorter and curvature stresses are larger. Sintering occurs over a range of temperatures, but is accelerated as the particles approach their melting range. As diffusion accelerates at higher temperatures, sintering is manifested by bonding between contacting particles. Packed particles heated near their melting temperature bond together by sintering.
